
The Challenges of Harmonizing Metric and Imperial Standards in Cross-Border Product Design
By Sean ButlerThe Challenges of Harmonizing Metric and Imperial Standards in Cross-Border Product Design
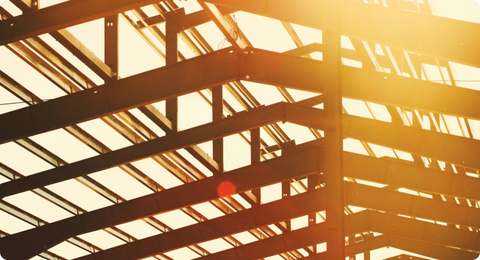
When designing products in China for sale in the United States, a persistent challenge is the harmonization of metric and imperial systems. The fundamental issue is obvious: Chinese manufacturers operate strictly in the metric system, while North American standards are based on imperial measurements. These differences create cascading challenges that affect everything from product sizes to pallet dimensions, shipping logistics, and consumer communication.
In one ongoing project for a portfolio company, which involves producing building materials for the North American market, we’ve encountered this issue firsthand. A key example is the 4 x 8 foot panels that are standard in North America. In China, these panels are produced as 1200 x 2400 mm. While 4 x 8 feet is technically 1219 mm x 2440 mm, Chinese manufacturers use the metric standard, leading to slight differences in size.
These size mismatches, alongside other subtle differences—often referred to as the gap between nominal and actual sizes—are common in exports from Asia and Europe to the U.S. These seemingly minor discrepancies have cascading effects throughout the supply chain.
Pallet Sizing: A Cross-Continental Challenge
The issue becomes even more complex when we factor in pallet sizes. In North America, 95% of goods are handled on pallets with at least one 48-inch dimension. However, Chinese manufacturers, accustomed to their domestic markets, often don’t understand the importance of aligning with North American pallet requirements. In China, building materials are typically crated, loaded onto trucks, and delivered directly to construction sites—no pallets required.
To them, making adjustments to accommodate a specific pallet size is an unnecessary complexity, even if it saves many hours of California-priced warehouse labor (roughly 10-12 times higher than Guangdong or Jiangsu warehouse labor).
By contrast, the export chain for North American markets is much more complex, and products must be palletized for several stages in the logistics process, including:
1. Manufacture of the product.
2. Packaging for export.
3. Loading into containers.
4. Transport to the port and loading onto ocean freight.
5. Ocean freight transport.
6. Drayage (short-distance transport) and delivery to a warehouse.
7. Receiving and putaway by the warehouse.
8. Creating a pick line for the warehouse.
9. Receiving a customer order.
10. A picker retrieves the required number of units from storage.
11. The order is consolidated and prepared for outbound shipment.
12. Outbound freight transport.
13. Final customer delivery.
For steps 7 through 13, the products must be palletized, and the 48-inch pallet size is critical to the efficient functioning of the North American warehouse and logistics system. Convincing Chinese manufacturers to adopt these requirements is an ongoing challenge. To them, making adjustments to accommodate a specific pallet size is an unnecessary complexity, even if it saves many hours of California-priced warehouse labor (roughly 10-12 times higher than Guangdong or Jiangsu warehouse labor).
Communicating Measurements to North American Consumers
Another challenge lies in communicating product measurements to North American consumers. Speaking in millimeters or offering product dimensions like “7 feet 11.25 inches” doesn’t work well in a market used to simple, round figures like 8 feet. While the metric system may be more precise, North American consumers have an ingrained preference for imperial measurements.
This discrepancy between systems creates confusion not only in product dimensions but also in installation and application processes. Whether it’s for building materials or consumer products, clear and relatable communication of size and dimensions is essential to avoid misunderstandings.
Container vs. Truck Dimensions: An Ongoing Dilemma
Another hidden complication is the difference in international container dimensions and North American trucking standards. Containers used in ocean freight are typically smaller than the trailers used in North American trucking, and the resulting space differences can lead to inefficiencies when unloading and redistributing goods.
Optimizing product design to fit perfectly in a container may require high-cost repacking to fit properly onto North American pallets and trucks. These space constraints can cause delays and add unnecessary costs to the logistics process, further complicating an already complex supply chain.
At the same time, being willing to compromise and accommodate the highly efficient Chinese manufacturing systems is crucial. Finding a middle ground where products can be designed efficiently for both Chinese manufacturing and North American logistics is key to minimizing costs and maximizing efficiency across the global supply chain.
A Successful Product Design
A successful product design requires patience from all sides, a willingness to educate and to be educated, and a capability to roll up the sleeves and do the Excel analysis, market research, and customer conversations to create a product that can be successfully manufactured, transported, marketed, and sold.
Navigating the Future of Global Standards
As businesses continue to operate in an increasingly globalized environment, the challenges of harmonizing metric and imperial standards will persist. For those of us working on projects that require cross-continental coordination—like our building material production for North America—these issues go far beyond a simple misunderstanding of measurements. They ripple through manufacturing, logistics, warehousing, and ultimately consumer satisfaction.
Finding ways to educate manufacturers on North American standards, ensuring alignment on pallet and packaging requirements, and developing clear communication for both logistics partners and end consumers are all essential steps in bridging the gap between these two systems.